Maintaining hydraulic cylinders is crucial to ensure their smooth and safe operation. Here are some key maintenance procedures:
- Regular Inspections: Conduct routine visual inspections for leaks, damage, or wear. Check for any signs of hydraulic fluid leakage, dents, scratches, or corrosion on the cylinder body or rod.
- Cleanliness: Keep the hydraulic cylinder and surrounding components clean from dirt, debris, and contaminants. Regularly wipe down the cylinder to prevent foreign particles from entering the seals and causing damage.
- Seal Inspection and Replacement: Check the seals and O-rings for wear, cracks, or damage. Replace them if there are signs of deterioration to prevent hydraulic fluid leakage.
- Lubrication: Apply appropriate lubrication to the cylinder rod and seals as recommended by the manufacturer. Lubrication helps maintain proper sealing and reduces friction, extending the cylinder’s lifespan.
- Rod Surface Maintenance: Inspect the rod surface for nicks, scratches, or scoring. Smooth out any minor imperfections that could damage the seals or cause leakage. Consider re-chroming or replacing severely damaged rods.
- Pressure Testing: Periodically conduct pressure testing to ensure the hydraulic cylinder can handle the required pressures without leaking or malfunctioning.
- Alignment and Mounting: Check the alignment and mounting of the hydraulic cylinder. Misalignment can cause undue stress and premature wear. Ensure the cylinder is correctly mounted and aligned with other components.
- Operational Checks: Regularly operate the cylinder through its full range of motion. This action helps identify any irregularities or sticking points in the cylinder’s movement.
- Fluid Condition and Filter Maintenance: Monitor the hydraulic fluid quality and regularly change filters according to the manufacturer’s recommendations. hydraulic cylinder suppliers Clean fluid and proper filtration prevent contamination and maintain optimal performance.
- Component Replacement: Replace worn or damaged components promptly. This includes seals, rods, bearings, or any other parts showing signs of wear to prevent further damage and ensure safe operation.
Adhering to a regular maintenance schedule, following manufacturer guidelines, and conducting proactive inspections are essential to ensure hydraulic cylinders operate smoothly, efficiently, and safely, extending their lifespan and optimizing excavator performance.
Are there specific safety protocols or guidelines to follow when dealing with the hydraulic cylinder in different work environments or scenarios?
Absolutely, adhering to safety protocols is crucial when dealing with hydraulic cylinders in various work environments or scenarios. Here are specific safety guidelines:
- Personal Protective Equipment (PPE): Wear appropriate PPE such as safety goggles, gloves, and protective clothing to safeguard against potential hydraulic fluid leaks, debris, or any unexpected releases of pressure.
- Hydraulic System Shutdown: Prior to any maintenance or inspection, shut down the hydraulic system and relieve pressure by activating controls to lower the hydraulic cylinder or using relief valves.
- Lockout/Tagout Procedures: Implement lockout/tagout procedures to prevent accidental activation of the hydraulic system while work is being performed on the cylinder.
- Stability and Support: Ensure the excavator or machinery is properly stabilized and supported before conducting any work on the hydraulic cylinder to prevent tipping or movement.
- Correct Tools and Equipment: Use appropriate tools and equipment recommended by the manufacturer for maintenance or repairs to avoid damage to the cylinder or components.
- Handling Heavy Components: Hydraulic cylinders can be heavy. Use lifting equipment or assistance when handling heavy components to prevent strain or injury.
- Avoid High-Pressure Hazards: Never disconnect hydraulic lines or components under pressure. Relieve pressure before any disassembly to prevent sudden release of hydraulic fluid.
- Safe Working Distance: Maintain a safe distance from the hydraulic cylinder when it’s under load or pressure to avoid potential injury in case of failure.
- Regular Inspections: Periodically inspect hydraulic lines, fittings, and connections for leaks or damage. Address any issues immediately to prevent safety hazards.
- Follow Manufacturer Guidelines: Always refer to the manufacturer’s guidelines and equipment manuals for specific safety protocols and procedures relevant to your equipment model.
- Emergency Procedures: Ensure operators and maintenance personnel are familiar with emergency shutdown procedures and are trained in responding to hydraulic system failures or accidents.
- Training and Awareness: Provide proper training to personnel working with hydraulic systems. Ensure they understand the risks involved and are aware of safety procedures.
By strictly adhering to these safety protocols and guidelines, workers can minimize the risks associated with hydraulic cylinder operations, ensuring a safer working environment and reducing the likelihood of accidents or injuries.
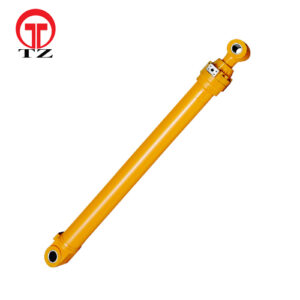